-
Contiweb Digital Fluid Applicator
-
Applying fluids for smooth processing and enhanced product quality
-
Removes curled paper edges and paper waviness
The smooth way to achieve top quality
Benefits
- The DFA uses contact rollers to apply moisture to the paper evenly
- The amount of moisture can be set and controlled very precisely for each side of the paper
- Uses tap water, so no need for specially prepared osmosis water or deionized (DI) water
- Can optionally mix pure silicone oil with the tap water to protect against damage to the printed matter in the finishing line
- Easy to operate via a touchscreen HMI
- Can be controlled by central press software
- Machine is quick and easy to install
- Compatible with all brands of web inkjet printing presses.
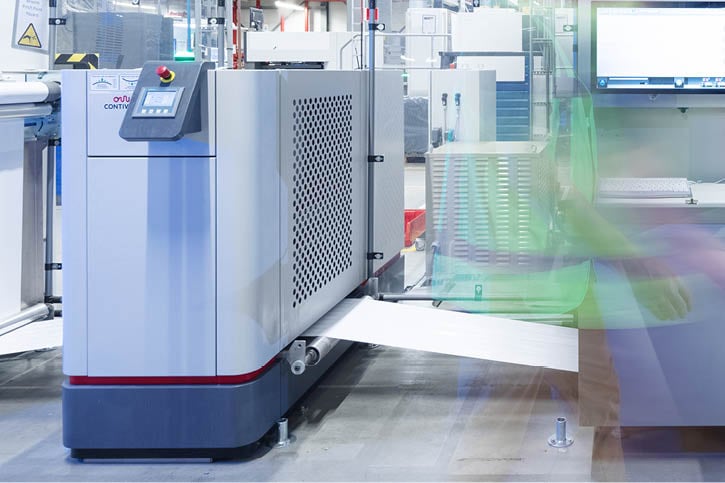
Drying the paper can damage it
Drying printed paper is a critical step in the web inkjet production process. However, a huge amount of heat is rapidly applied to the water-based inks to meet the market need for ever faster production. During this process, the temperature of the paper easily exceeds 100°C or 212°F. This not only causes the moisture from the ink to evaporate, but also the moisture in the paper. As a result, after printing the paper often has a moisture content of less than 1%.
Paper with a low moisture content is weaker and therefore prone to breaks or cracks. The paper will also tend to absorb moisture due to its hygroscopic properties. If this happens in an uncontrolled manner, wavy paper and curling edges are inevitable. This causes inferior and unmarketable product quality and can lead to problems like jams in the finishing line.
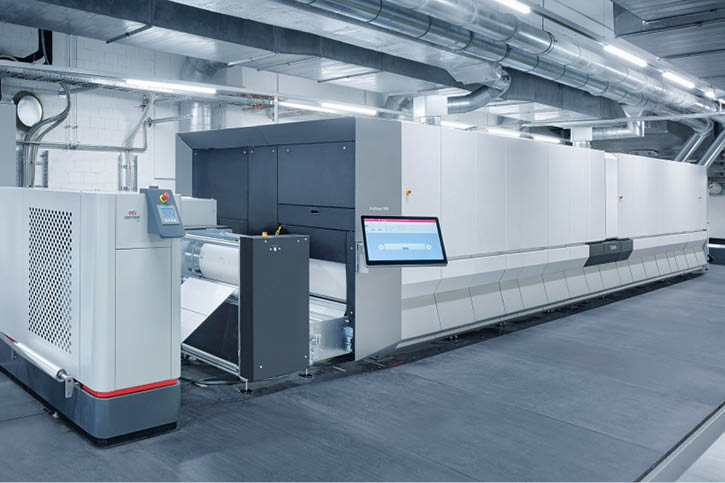
Controlled remoistening
The DFA is a standalone remoistening system for web inkjet presses that applies moisture to the paper web to prevent curled paper edges and waviness. The result is is increased product quality and smoother processing in subsequent equipment. The DFA also offers the option to mix in silicone oil, which protects the printed material from damage caused by finishing systems. This Contiweb system is compatible with all inkjet web presses.
The DFA uses steel rollers that are mechanically pressed against the paper web to apply moisture. Textile sleeves are pulled over the steel rollers to ensure an even distribution of moisture. This is critical because it ensures maximum reduction of waviness and warping of the paper edges after printing and drying of the paper web. This method eliminates the undesirable cockling effect.
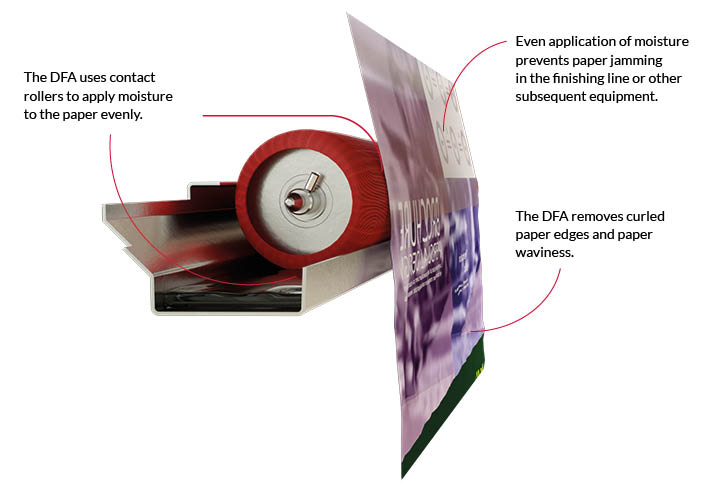
Tap water
Contiweb's DFA remoistening system uses tap water, and so does not need specially prepared osmosis water or deionized (DI) water. The machine mixes water, surfactant and optionally silicone oil directly in the applicator trays immediately before it is applied to the printed web. This ensures uniform remoistening, and reproducible results. The operator only needs to enter the desired oil and water coverage in mg/m² for each side of the paper web on the touch screen HMI, and the control do the rest. Settings can be easily stored and recalled.
All functions are available in a contained unit, installation and commissioning are based on a plug and play principle. The DFA is compatible with all inkjet web presses.
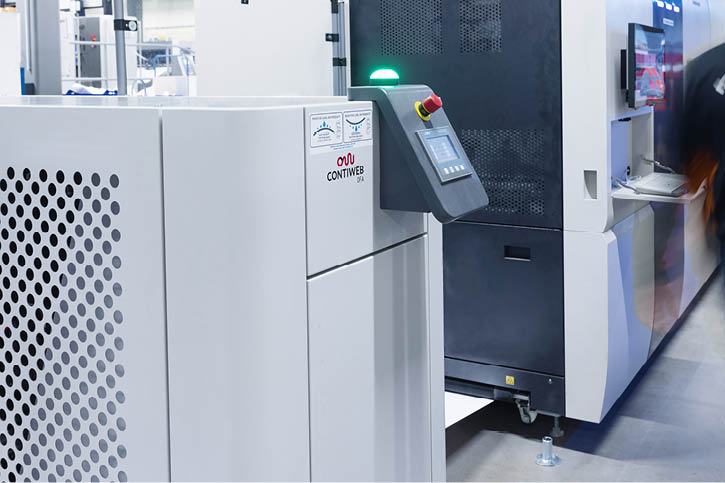
Silicone application
With inline finishing configurations increasing in popularity in web inkjet, the DFA's option to add silicone is gaining importance. Many finishing systems use a lot of moving parts like rollers and wheels which, in time, can leave unwanted scratches and scuffs. These can cause image damage, reducing the value of the printed product.
Contiweb has extensive knowledge of moisture and silicone application in web printing. The experience we've gained in the heat set web offset industry has been successfully applied to inkjet. Contiweb has an installed base of more than 600 remoistening and silicone applicators at top quality printers around the world.
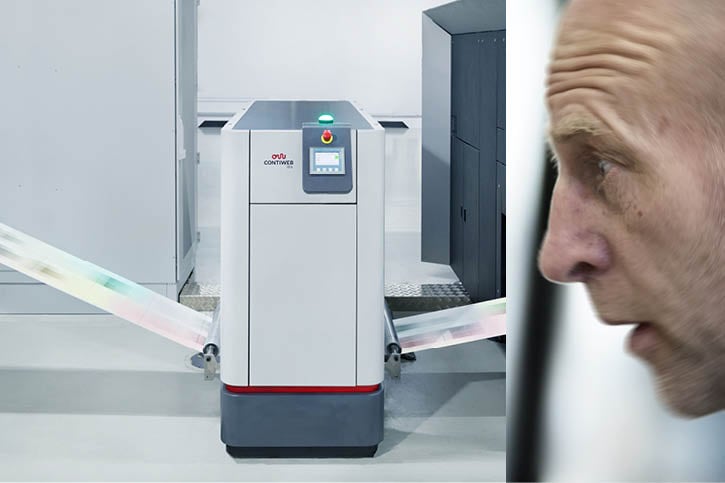
Frequently Asked Questions
Below you find the answers to some commonly asked questions about this equipment.
Due to the use of water-based inks in roll-fed inkjet presses and the high printing speeds they can achieve, there is a need to dry prints quickly and at high temperatures. However, this fast and hot drying process can give rise to several problems.
The printed material may become wavy, making it difficult for signatures to lie flat. Another problem that can occur is the curling of paper edges. Both problems can create challenges in the finishing line. They may lead to congestion and downtime. Also, the overall appearance and quality of the final product may be impacted. In the worst case scenario, the customer may reject the products.
To gain more insight into these problems, you can refer to this blog post, which provides further details on these issues and their potential impact on printed materials.
The Contiweb Digital Fluid Applicator utilizes fabric sleeves for several advantageous reasons. Fabric sleeves are carefully crafted with a distinctive engraved pattern on their surface. These engravings consist of precisely sized and spaced cells, forming a meticulously controlled system for storing and releasing moisture. The result is an exceptional distribution of fluids across the paper web, ensuring uniform coverage.
Moreover, textile sleeves possess inherent resilience and compression properties. When pressure is applied due to unevenness of the printed paper, the sleeve undergoes a slight deformation. This adaptability helps maintain a consistent contact surface between the sleeve and the paper, enabling reliable fluid transfer. By accommodating variations in the paper surface, textile sleeves contribute to consistent and accurate application of fluid, ultimately improving overall printing performance.
The durability of fabric sleeves in the Contiweb Fluid Applicator can vary depending on the specific printing application. While fabric sleeves offer excellent and uniform fluid coverage on paper, they are not immune to wear. The lifespan of fabric sleeves is highly dependent on the operating conditions and printing practices employed.
Different printers experience varying durations of sleeve usage. Some printers may utilize the same fabric sleeve for several months without requiring replacement, while others may find it necessary to replace sleeves after only a few weeks of use. The longevity of fabric sleeves is influenced by factors such as print volume, print speed, substrate characteristics and ink fluid formulations.
Replacing the fabric sleeves is a straightforward procedure. The roller containing the worn sleeve is detached from the Digital Fluid Applicator, the worn sleeve is cut open and removed from the roller. The new fabric sleeve is then shrunk tightly around the roller with hot water and the roller is reinstalled into the machine. As the roller rotates through the pan and becomes moistened, it is ready to resume its function. Printers who do not want to lose any production time, prepare an extra set of rolls with new sleeves.
Contiweb provides convenient access to replacement sleeves through the Contiweb Parts Webshop.
With inline finishing configurations increasing in popularity in web inkjet, the DFA's option to add silicone is gaining importance. Many finishing systems use a lot of moving parts like rollers and wheels which, in time, can leave unwanted scratches and scuffs. These can cause image damage, reducing the value of the printed product.
Contiweb has extensive knowledge of moisture and silicone application in web printing. The experience we've gained in the heat set web offset industry has been successfully applied to inkjet. Contiweb has an installed base of more than 600 remoistening and silicone applicators at top quality printers around the world.
The purpose of silicone application is to minimize marking or scuffing during post-processing equipment handling. The protective effect of the silicone oil is temporary. Within a day, the silicone oil is completely absorbed by the paper. Once absorbed, the silicone oil no longer serves its protective function and has no impact on the appearance of the final product. The application of silicone oil by the Contiweb Digital Fluid Applicator does not affect the remoistening.
Surfactant and silicone oil are not provided as standard with the purchase of a Digital Fluid Applicator. They can be sourced from various suppliers of printing consumables.
Spare parts for Contiweb Digital Fluid Applicators are conveniently available in the Contiweb Parts Webshop. Sign up for an account and gain free access to Contiweb machine manuals and parts books, saving you valuable time by filtering your search for specific machine parts.
Plus, explore our Uptime Kits, specially curated with essential components to minimize downtime in the event of breakdowns, ensuring you have the necessary parts readily available in your own facility. Streamline your maintenance and keep your operations running smoothly with Contiweb.
Trusted by
Would you like to know more?
If you are interested in Contiweb's remoistening solutions and you would like to know more, then please don't hesitate to contact us!
Sales contact
Rob Bosman
Sales Director
+31 6 51 20 27 55
sales@contiweb.com
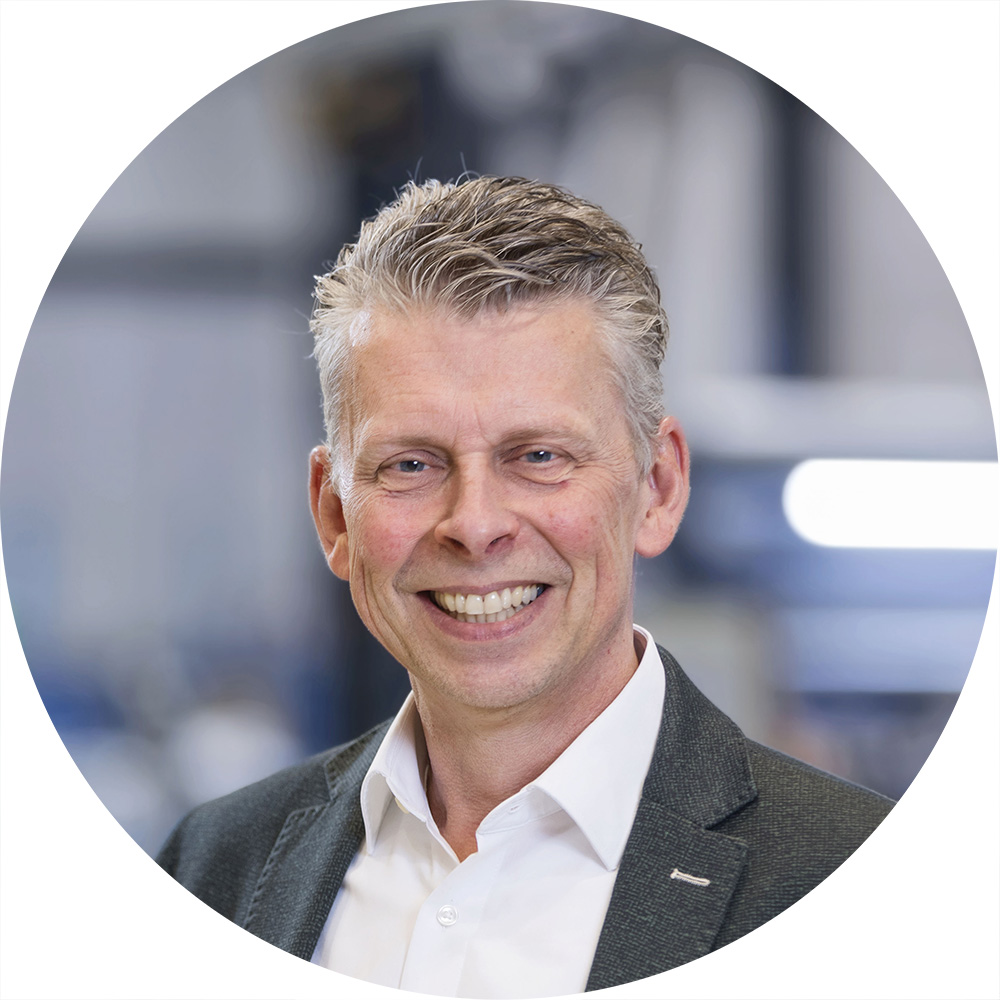