-
CP-N Non-Stop Unwinding Equipment
-
Automatically change paper reels without production stop
Enhanced productivity and ergonomics
The Contiweb CP-N Non-Stop Unwinder ensures uninterrupted production in high-speed environments where reels of paper, paperboard, cardboard, film, or foils are unwound. It enables seamless reel changes without halting the production process, boosting output, reducing operational costs, and optimizing resource allocation—all while improving workforce well-being.
- Automatic reel changes for continuous, uninterrupted production.
- Cost-saving automation for high efficiency.
- Enhanced workforce safety and ergonomics.
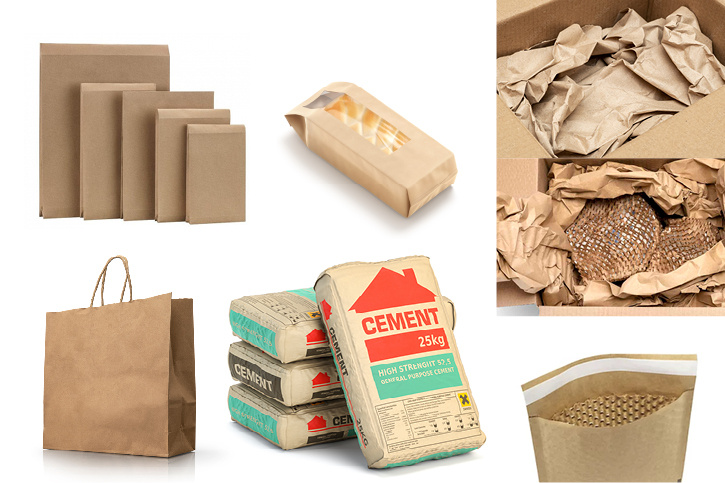
Benefits
- Seamless, automatic reel changes for uninterrupted production.
- Optimizes production output and efficiency.
- Allows operators to prepare the next reel during production.
- Offers exceptional process flexibility to handle diverse materials.
- Ensures smooth and precise splicing.
- Simple operation with minimum training.
- Reduces manual handling, enhancing safety and ergonomics.
- Ensures operator safety and prevents workplace accidents.
- Requires minimal maintenance and ensures a long equipment lifetime.
Features
- Automatic-splicer with two reel positions.
- Robust and sturdy design.
- Maximum winding speed: 5.5 m/s.
- Paper weight range: 30 to 350 g/m².
- Paperboard thickness: up to 18 pts.
- Film thickness range: 5-70 µm.
- Easy reel loading and splice preparation in only 2 minutes.
- Intuitive touchscreen interface (HMI).
- Core chucks instead of reel shaft.
- Comprehensive safety compliance: CE, BG, UL, and CSA standards.
- Optional: Integration of infeed systems and web guiding for enhanced precision.
- Optional: Advanced transport systems to streamline workflows.
- Optional: Comprehensive aftermarket services, including remote and on-site support.
Continuous production without interruption
Automated solutions, like the Contiweb CP-N Non-Stop Unwinder, address these challenges by unlocking new levels of efficiency.
Increased cost-effectiveness and optimized resource allocation
Contiweb auto-splicers significantly reduce downtime during reel changes, enabling continuous production and lowering the cost per unit. By utilizing production time more effectively, manufacturers can minimize operational costs and allocate resources more efficiently.
Beyond reducing delays, automated splicing systems also address a pressing issue faced by many industries: labor shortages. By automating the labor-intensive process of manual reel handling, Contiweb’s solutions reduce the reliance on larger workforces. This ensures high productivity even in environments where skilled labor is limited.
Automation not only lowers labor costs but also allows employees to focus on high-value tasks, such as quality control, process optimization, and equipment monitoring. This shift improves resource utilization and enhances employee satisfaction by reducing repetitive and physically demanding tasks.
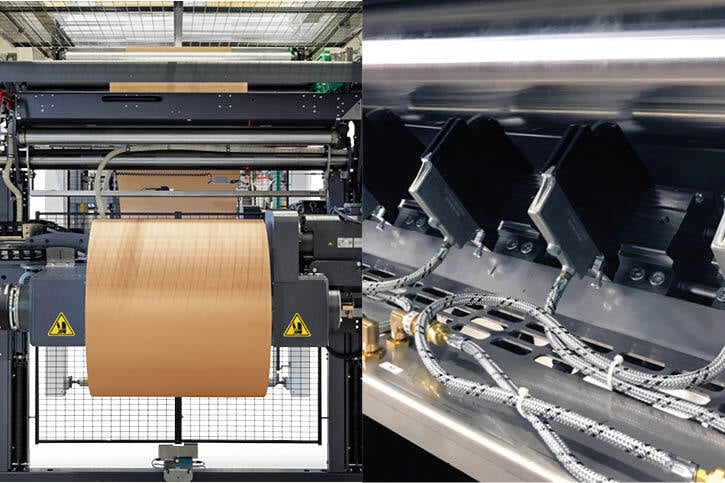
Improved ergonomics for workforce wellbeing
In addition to enhancing operational efficiency, Contiweb auto-splicers promote workplace ergonomics by alleviating physical strain on workers. The Contiweb CP-N Non-Stop Unwinder is equipped with core chucks that eliminate the need for manual lifting of heavy paper reels or core shafts—tasks that can exceed 30 kg. This ergonomic advantage significantly reduces the risk of injuries and physical stress, fostering a safer and healthier work environment.
By prioritizing employee well-being, Contiweb not only boosts productivity but also contributes to long-term workforce health and morale. This combination of efficiency and care makes Contiweb non-stop auto-splicers a preferred choice for manufacturers seeking sustainable and ergonomic production solutions.
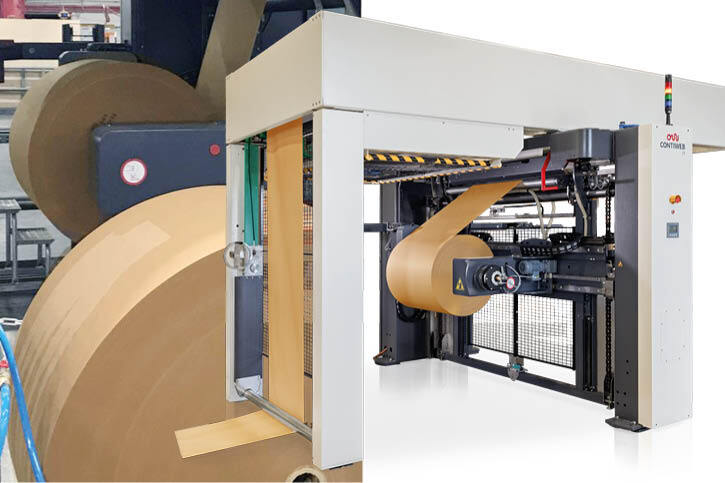
Zero-speed splicing
The CP-N works as a horizontal zero-speed compensator splicer, but with fully automatic splicing as well as integrated infeed as standard.
The proven Contiweb zero-speed festoon design brings the running web and the new web to a halt during the splice cycle while the press is fed from the integrated festoon.
Performing the splice at zero speed minimizes all dynamic forces on the web. The operation is therefore very forgiving of variations in splice preparation, such as operator skills and web quality. A lap splice is standard, and the CP-N can optionally perform one or two-sided butt splices.
The splice can be made at all reel diameters, and the zero speed principle minimizes all dynamic forces on the web with every splice. That offers maximum flexibility for changing substrate or web width easily, including the smallest rest reels.
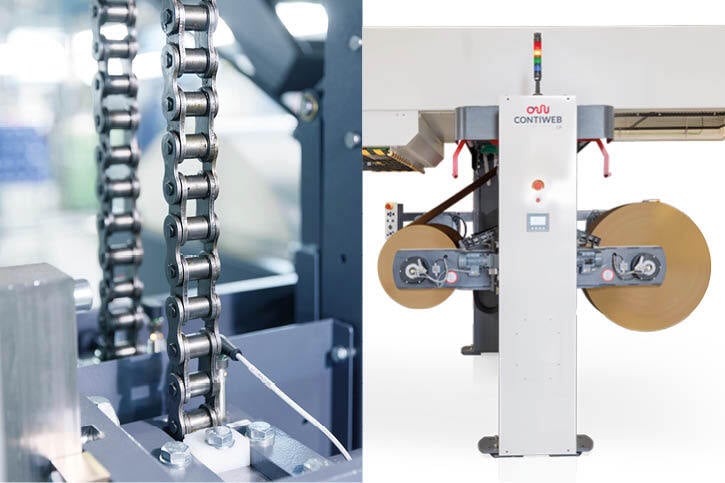
Would you like to know more?
If you are interested in optimizing your production using the Contiweb CPN, then please don't hesitate to contact us.
Sales Contact
Rob Bosman
Sales Director
+31 6 51 20 27 55
sales@contiweb.com
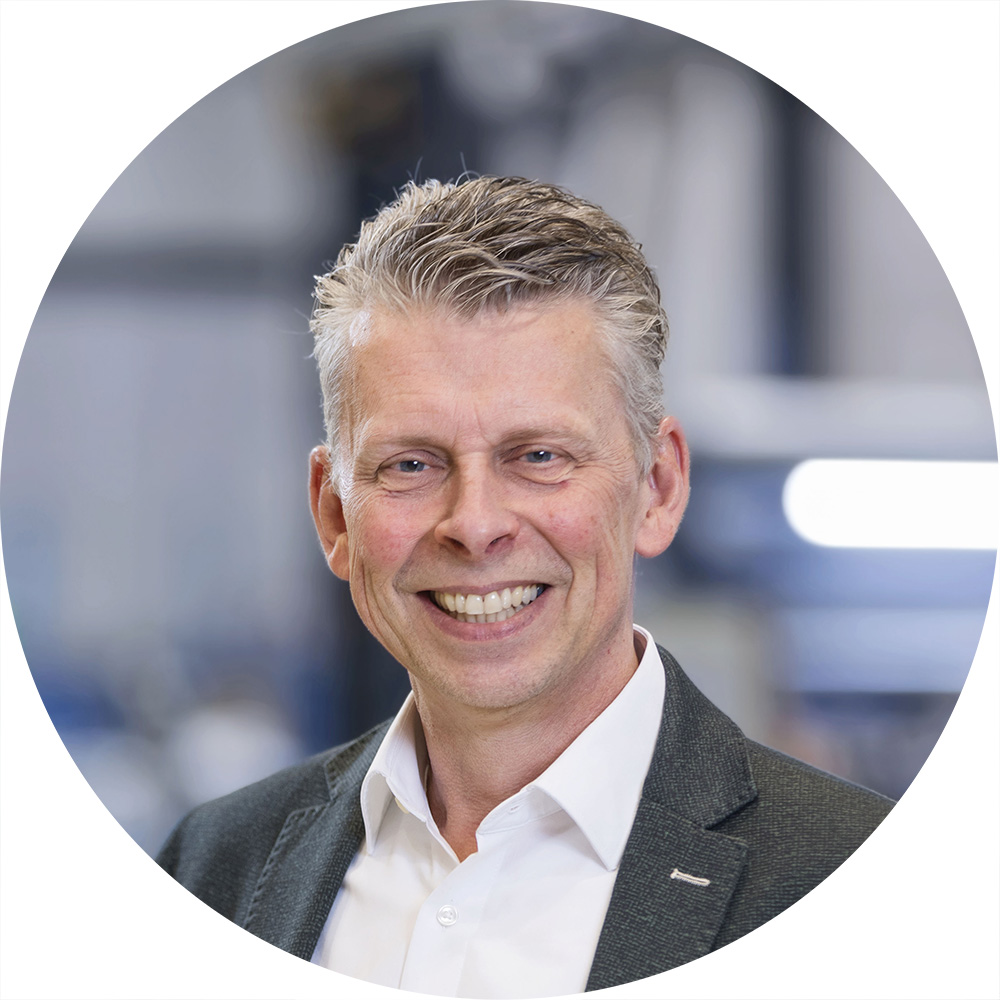