-
Contiweb
Variable Coater for post-coating -
Quick web width change without exchange of components
-
Automatically adjust the coating layer without operator interference
Realize the full potential of web inkjet printing
The Contiweb Variable Coater (VC) is a high-end system that can post-coat paper after printing it or prime paper before. Both post-coating and priming can be done near-line or in-line. The VC uses the patented automated metering technology to very precisely apply the coating layer on the web, causing no standstill during a web width change or when changing the coating layer thickness. You can queue small print jobs with ever-changing coating layer and web width, without costly interruptions for replacing machine parts.
Benefits
- Post-coating adds varnish as a protective layer to improve the durability of the printed product
- Matt or gloss varnish improves the appearance of the printed product
- Thanks to the patented automated metering technology, the coating thickness can be adjusted very precisely. It is accurate, repeatable and reproducible
- More than 15% cost savings on post coatings due to precise volume tuning
- Quick web width and coating coverage change without exchange of machine components
- The VC can be controlled digitally, from the press console
- Recipes for coating jobs can be saved and easily called up
- No purchase, storage or cleaning costs for sleeves and anilox rollers
- The VC can also be used for priming to make offset paper fit to handle inkjet inks
Features
- Duplex flood coater (can be used simplex)
- In-line (priming or post-coating) or near-line (priming or post-coating)
- Aqueous based coatings for good environmental performance
- Two operating speeds: up to 165m/min or 330m/min
- Fully variable web width
- 60-250 g/m² paper
- 2-6 g/m² wet coating coverage for post-coating
- 1-3 g/m² wet coating coverage for priming
- Uses patented metering technology
No roller or sleeve changes
The Contiweb Variable Coater needs no roller changes to change the coating weight and no sleeves to change the web width. The machine uses a simple three-roller flood coating system, where the web travels vertically between the front and back cassettes. Each station has a rotating metering roller that picks up the coating fluid from the reservoir, transferring it onto a smooth stainless steel doctor roller and then to the rubber coated transfer roller which runs the speed of the web. By changing nip pressure the thickness of coat weight can be adjusted. The cleverly designed alignment of the rollers ensures a homogeneous coating coverage and compensates for all unevenness.
The duplex flood coater tunes the coating amount of both paper sides on the run. It can be used simplex, too. All nips and rollers speeds are independently adjustable, so the volume of coating transferred is precisely and controllable.
Precise volume tuning
The Variable Coater is uniquely flexible, and the coating thickness can be adjusted very precisely on both sides of the paper, based on selected coverage. This can be done independently of each other and "on the fly" during production, without machine reconfiguration or downtime. The Variable Coater can process paper with different web widths, without physical interference of an operator.
Most existing coaters use flexo technology with a range of aniloxes and sleeves to vary web width and coating weight as required. That limits the adjustability and causes unwanted interruptions, though. It also means additional investment in anilox rollers, along with higher operating costs due to cleaning and storage.
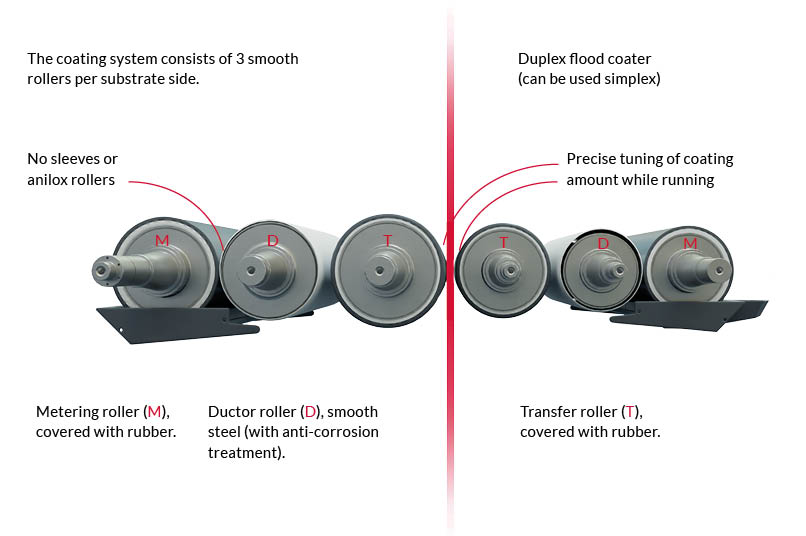
Post-coating improves durability
Post-coating can boost quality by adding a gloss or matt coating to the printed items. It also protects items like postcard mailers that could otherwise be damaged during mail handling. For self-mailers, the addresses are printed on the items themselves, so post-coating prevents them for becoming unreadable.
The coating thickness can be adjusted very precisely, and varnish consumption can be reduced by around 15% compared to conventional coaters. In this way, the coating coverage can be tuned to a minimum per production, preventing overspending on varnish.
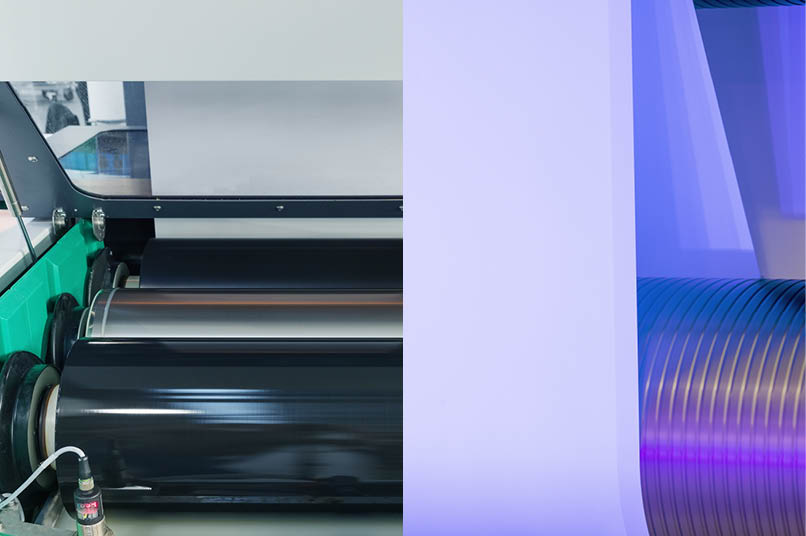
Frequently Asked Questions
Below you find the answers to some commonly asked questions about this equipment.
Post-coating can boost quality by adding a gloss or matt coating to the printed items, enhancing the look and feel. It also protects items like postcard mailers that could otherwise be damaged during mail handling. For self-mailers, the addresses are printed on the items themselves, so post-coating prevents them for becoming unreadable.
The Contiweb Variable Coater is a closed-loop controlled system designed to revolutionize coating application. Powered by our patented automated metering technology, this advanced system ensures the precise and optimal amount of coating is applied to the web, eliminating the risks of overcoating or undercoating.
Flexibility is at the core of the Contiweb Variable Coater. Adjusting to changing web widths or coating layers is now a seamless process. Thanks to its innovative design, you can seamlessly transition between different web widths and coating requirements without any machine standstill. This means you can effortlessly queue small print jobs with varying coating layers and web widths, eliminating costly interruptions for replacing machine parts.
Automation lies at the core of Contiweb's product strategy and development programs. Drawing on its expertise in heat-set web offset printing, Contiweb recognizes the significance of interconnected equipment that shares process information to achieve high-level automation. In today's world of web inkjet printing, a similar approach is essential.
With regards to the Variable Coater, depending on press requirements and communication capabilities, Contiweb will design an interface that facilitates seamless communication between the press and central control from the press console. This tailored interface ensures smooth integration and optimal performance based on the specific requirements and capabilities of the printing press.
In situations where the Variable Coater is not installed inline with a press, Contiweb takes steps to establish an interface with both the unwinder and rewinder units.
Today only aqueous based coatings can be used in the Contiweb Variable Coater. Aqueous based coatings are generally more affordable compared to UV coatings, making them a cost-effective option for many print projects. Also, they are more environmentally friendly due to their lower VOC content, water-based formulation, reduced energy requirements, easier waste disposal, and better regulatory compliance.
There is a wide range of manufacturers offering aqueous-based coatings and you are free to select the supplier that aligns best with your preferences and requirements.
While UV coatings are still the preferred choice for applications requiring extremely high gloss and reflectivity, advancements in aqueous coating technology have significantly improved their gloss capabilities. Coating manufacturers have developed specialized aqueous coatings that can achieve gloss levels closer to those achieved by UV coatings. These advancements provide more options for achieving desirable gloss rates with aqueous-based coatings.
Spare parts for the Contiweb Variable Coater are conveniently available in the Contiweb Parts Webshop. Sign up for an account and gain free access to Contiweb machine manuals and parts books, saving you valuable time by filtering your search for specific machine parts.
Plus, explore our Uptime Kits, specially curated with essential components to minimize downtime in the event of breakdowns, ensuring you have the necessary parts readily available in your own facility. Streamline your maintenance and keep your operations running smoothly with Contiweb.
Would you like to know more?
If you are interested in Contiweb's post-coating solutions and you would like to know more, then please don't hesitate to contact us!
Sales contact
Rob Bosman
Sales Director
+31 6 51 20 27 55
sales@contiweb.com
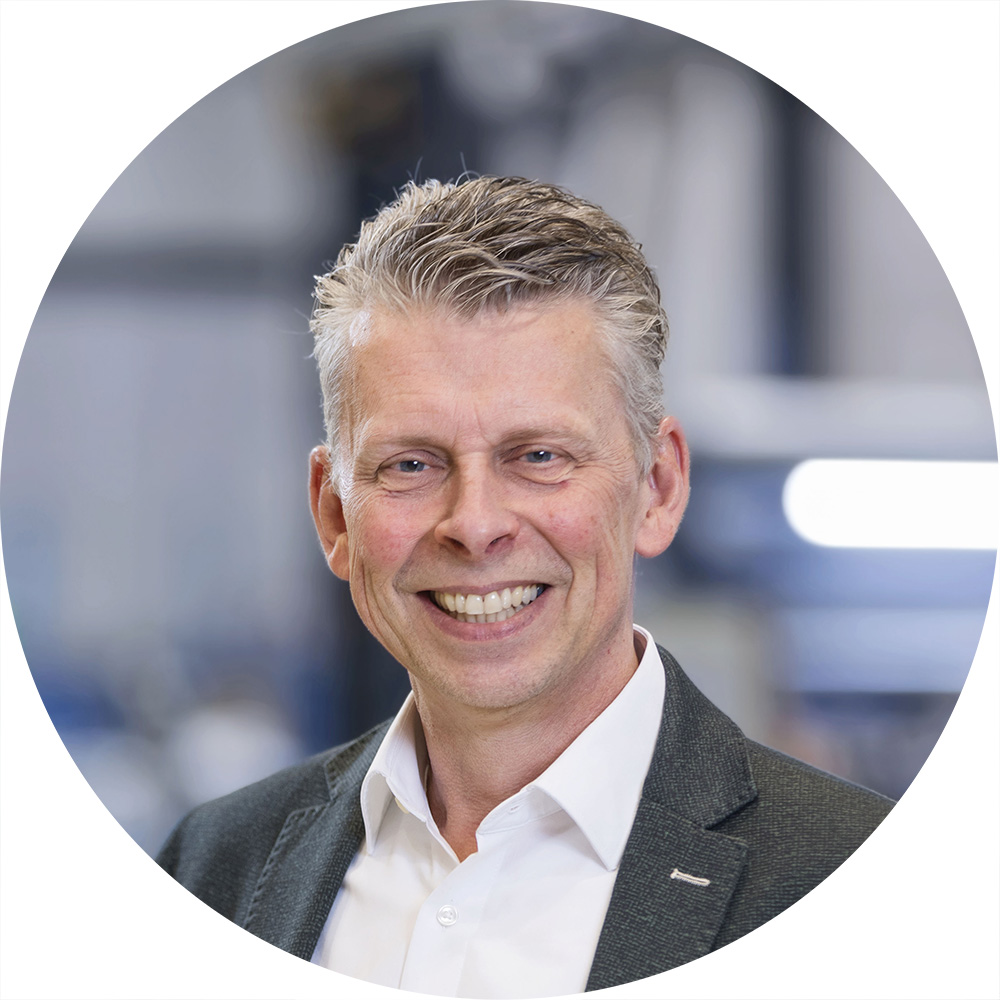