-
Contiweb
Variable Coater for priming -
Now you can use low-cost offset paper
-
The versatile cost-saving way to prime paper
Now you can use low-cost offset paper
Contiweb's Variable Coater lets you use standard offset paper that you can treat yourself, achieving high-quality print results with about 20% ink savings, and up to 30% savings in paper costs. The huge paper volumes treated give a payback period for the machine of between one and two years. Printers can use their existing presses more effectively and develop additional, profitable business streams without investing in expensive new presses.
Benefits
- The Variable Coater's priming improves the quality of the printed product (and opens up new markets)
- Save up tp 30% on paper costs by using standard offset paper instead of paper mill treated inkjet paper
- Significantly reduce ink usage with the same or even increased colour density
- Thanks to the patented automated metering technology, the coating thickness can be adjusted very precisely. It is accurate, repeatable and reproducible
- Quick web width and coating coverage change without exchange of machine components
- The VC can be controlled digitally, from the press console
- Recipes for coating jobs can be saved and easily called up
- No purchase, storage or cleaning costs for sleeves and anilox rollers
Features
- Duplex flood coater (can be used simplex)
- In-line (priming or post-coating) or near-line (priming or post-coating)
- Aqueous based coatings for good environmental performance
- Two operating speeds: up to 165m/min or 330m/min
- Fully variable web width
- 60-250 g/m² paper
- 1-3 g/m² wet coating coverage for priming
- Uses patented metering technology
No roller or sleeve changes
The Contiweb Variable Coater needs no roller changes to change the coating weight and no sleeves to change the web width. The machine uses a simple three-roller flood coating system, where the web travels vertically between the front and back cassettes. Each station has a rotating metering roller that picks up the coating fluid from the reservoir, transferring it onto a smooth stainless steel doctor roller and then to the rubber coated transfer roller which runs the speed of the web. By changing nip pressure the thickness of coat weight can be adjusted. The cleverly designed alignment of the rollers ensures a homogeneous coating coverage and compensates for all unevenness.
The duplex flood coater tunes the coating amount of both paper sides on the run. It can be used simplex, too. All nips and rollers speeds are independently adjustable, so the volume of coating transferred is precisely and controllable.
Precise volume tuning
The Variable Coater is uniquely flexible, and the coating thickness can be adjusted very precisely on both sides of the paper, based on selected coverage. This can be done independently of each other and "on the fly" during production, without machine reconfiguration or downtime. The Variable Coater can process paper with different web widths, without physical interference of an operator.
Most existing coaters use flexo technology with a range of aniloxes and sleeves to vary web width and coating weight as required. That limits the adjustability and causes unwanted interruptions, though. It also means additional investment in anilox rollers, along with higher operating costs due to cleaning and storage.
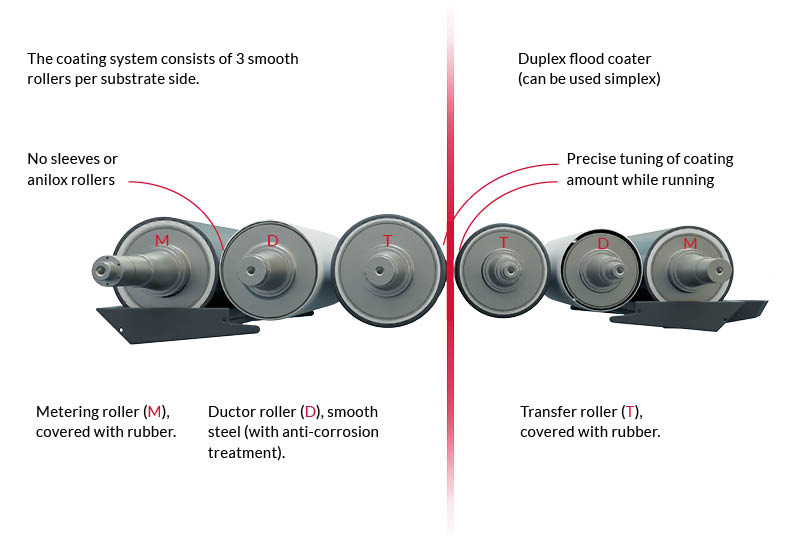
Improve quality and resolution
Producing products with a lot of ink coverage on a web inkjet press needs paper that does not absorb much ink. Paper mills do offer treated paper for inkjet printing, but this is expensive. There are relatively few variants on the market and their availability fluctuates. The paper mills will normally add a coating that gives the best average result with different kinds of inks, meaning that the coating is not optimized for each job.
The Variable Coater lets you prime low-cost offset paper in-house. This improves adhesion while significantly improving printability. It can be optimized for the specific ink that you are using, improving print quality and reducing ink consumption. Dot gain and ink absorbency are lower. That means using less ink, or the same amount of ink but higher density and so more attractive printing.
The Variable Coater can be set very precisely, so you can use a virtually unlimited range of paper types.
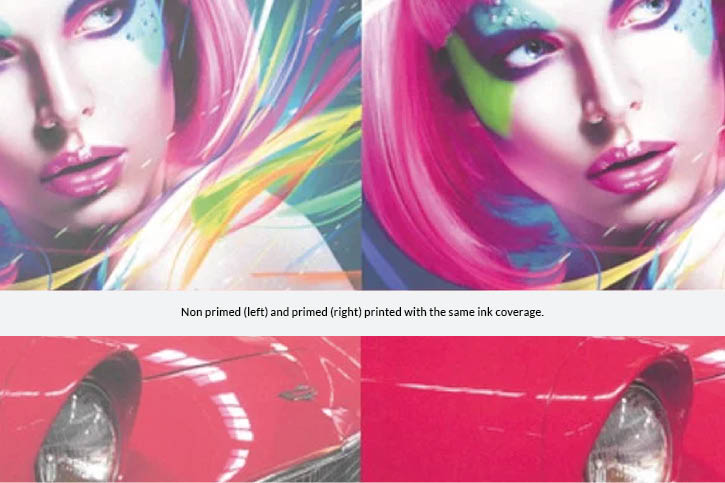
Frequently Asked Questions
Below you find the answers to some commonly asked questions about this equipment.
Contiweb's Variable Coater lets printers use standard offset paper that they can treat themselves, achieving high-quality print results and giving them access to an unlimited range of paper grades. It also saves them costs by eliminating the need to purchase expensive paper mill treated paper. Additionally, they won't be at the mercy of fluctuating paper availability, providing them with greater control and reliability.
Paper mills do offer treated paper for web inkjet printing, but there are relatively few variants available and their availability fluctuates. The paper mills normally add a coating that gives the best average result with different kinds of inks, meaning that the coating is not optimized for each job.
The Contiweb Variable Coater lets you prime low-cost offset paper in-house. This improves adhesion while significantly improving printability. It can be optimized for the specific ink that you are using, improving print quality and reducing ink consumption. Dot gain and ink absorbency are lower. That means using less ink, or the same amount of ink but higher density and so more attractive printing.
The Contiweb Variable Coater uses the patented automated metering technology to very precisely apply the coating layer on the web, causing no standstill during a web width change or when changing the coating layer thickness. You can queue small print jobs with ever-changing coating layer and web width, without costly interruptions for replacing machine parts.
Case studies show a payback period of less than two years. Depending on the customer, savings can include:
- Paper (affordable offset paper instead of expensive mill treated inkjet paper)
- Ink (reduced consumption)
- Handling (no cleaning costs of anilox and doctor blade, no additional personnel to exchange sleeves and anilox)
- Consumables (no replacements needed for sleeves or anilox)
Please contact us for a payback period calculation for your specific situation.
When the Contiweb Variable Coater is integrated inline with a web inkjet press, Contiweb will design an interface that enables seamless communication between the press and central control from the press console. In the case of standalone installation, Contiweb will establish an interface with both the unwinder and rewinder units.
Spare parts for the Contiweb Variable Coater are conveniently available in the Contiweb Parts Webshop. Sign up for an account and gain free access to Contiweb machine manuals and parts books, saving you valuable time by filtering your search for specific machine parts.
Plus, explore our Uptime Kits, specially curated with essential components to minimize downtime in the event of breakdowns, ensuring you have the necessary parts readily available in your own facility. Streamline your maintenance and keep your operations running smoothly with Contiweb.
Would you like to know more?
If you are interested in Contiweb's paper priming solutions and you would like to know more, then please don't hesitate to contact us!
Sales contact
Rob Bosman
Sales Director
+31 6 51 20 27 55
sales@contiweb.com
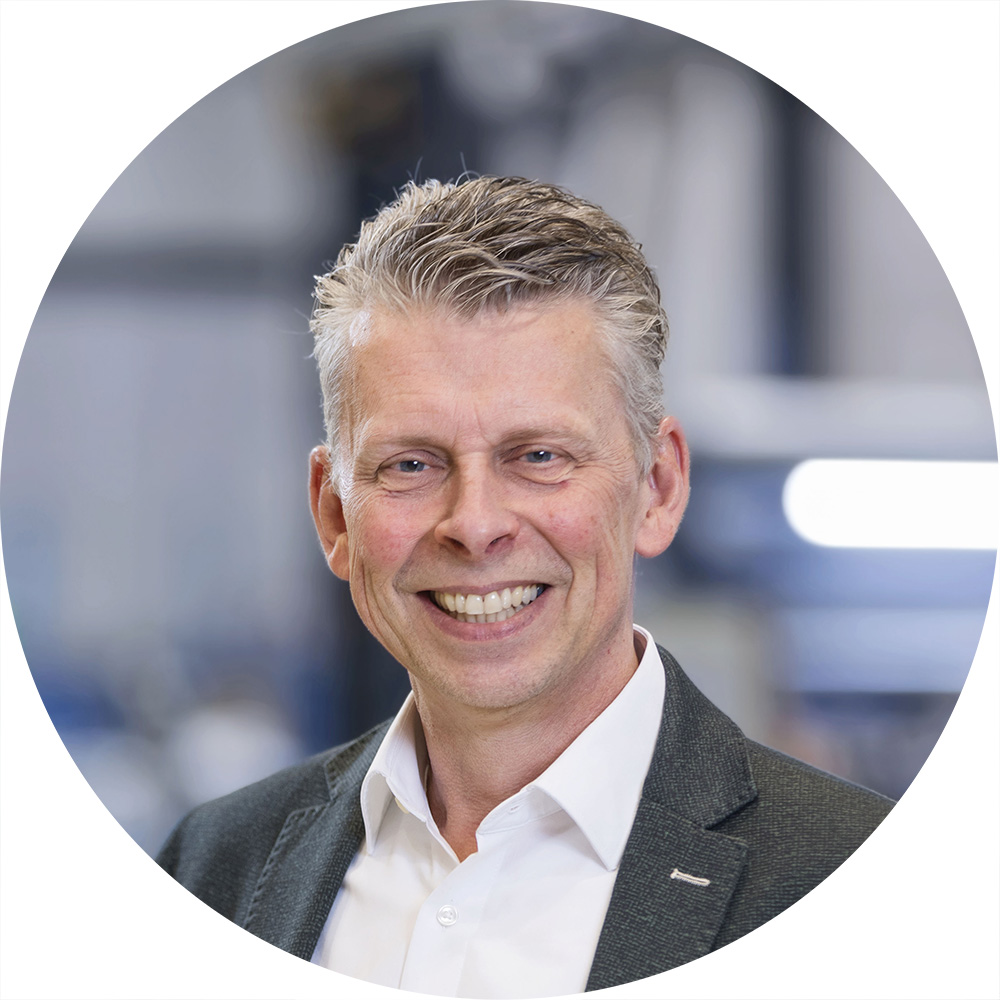