-
CD-N Non-Stop Unwinding Equipment
-
Keeps digital print jobs moving continuously
-
Automatically change paper reels without production stop
Keep digital print jobs moving continuously
Benefits
- Non-stop winding saves considerable production and labor hours
- Change reels and prepare splices during production, so avoiding production stops
- Preparing the splice is very easy and takes only two minutes. The splice performance is regularly and repeatably 99.8% or higher
- You can splice over to papers of different web widths, coatings and weights. This is very useful for short, fast-changing jobs. It is also easy to use rest reels, and there is no restriction on the diameter of the new or used reel for splice performance
- If your press can accept it, Contiweb non-stop winding equipment sends a signal to your press when a splice is coming. This way the press can lift the print heads. The Contiweb equipment will even send a signal if it recognizes a splice made by the paper mill! Contact Contiweb for more information.
- The lift arms of the Contiweb equipment can move up and down, allowing the reel to be loaded from the ground. This operation is ergonomic, and requires no lifting crane
- Additional advantages are: fewer mistakes when preparing the splice, less chance of losing the web completely out of the engines (time pressure of production). Less waste by cutting unnecessary white paper, fewer startup problems, energy savings by quick change over.
Features
- Horizontal festoon for zero-speed splicing
- Lap splice as standard. Single sided butt splice optional
- Arms that lift the reels up and down from the loading platform
- No reel shafts required
- Easy to use Human Machine Interface
- Compatible with all web inkjet presses
- Paper weight from 40 to 300 g/m2. Optionally to 350 g/m2
- Maximum winding speed 5.5 m/s (1080 f/m).
- CD-N non-stop unwinder available in 22” (560mm), 42" (1100mm), 30” (770mm) and 61”(1530/1550mm) versions
- CR-N non-stop rewinder available in 22” (560mm) and 42” (1100mm) versions.
CD-N non-stop unwinder
The CD-N works as a horizontal zero-speed compensator splicer, but with fully automatic splicing as well as integrated infeed as standard.
The proven Contiweb zero-speed festoon design brings the running web and the new web to a halt during the splice cycle while the press is fed from the integrated festoon.
Performing the splice at zero speed minimizes all dynamic forces on the web. The operation is therefore very forgiving of variations in splice preparation, such as operator skills and web quality. A lap splice is standard, and the CD-N can optionally perform one or two-sided butt splices.
The splice can be made at all reel diameters, and the zero speed principle minimizes all dynamic forces on the web with every splice. That offers maximum flexibility for changing paper type or web width easily, including the smallest rest reels.
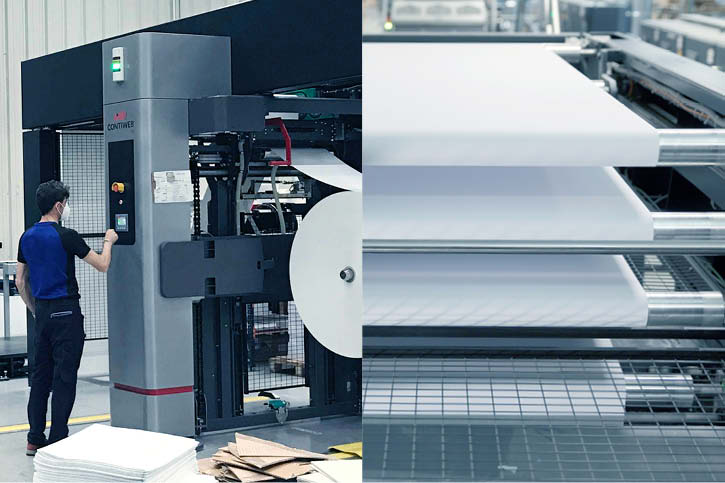
Easy reel loading and splice preparation
Reel loading and splice preparation for automatic splicing using the Contiweb CD-N non-stop unwinder are quick and straightforward tasks that only take 2 minutes to complete. These tasks can be easily performed in a situation safe for the operator, even while production is ongoing. The operator's involvement is minimal and involves applying a linear adhesive tape for the straight-tape splice on the paper. The time required for splice preparation is limited to the actual preparation process itself.
Here, you can find a video demonstrating the reel loading and splice preparation process. The video demonstrates the overlap splice preparation. You can watch the butt splice preparation here.
Short payback period
By eliminating an enormous number of lost production hours when using manual winding equipment, non-stop winding equipment normally pays for itself very quickly.
Use our easy calculator tool for an indication of the payback period and determine whether you can benefit from non-stop winding.
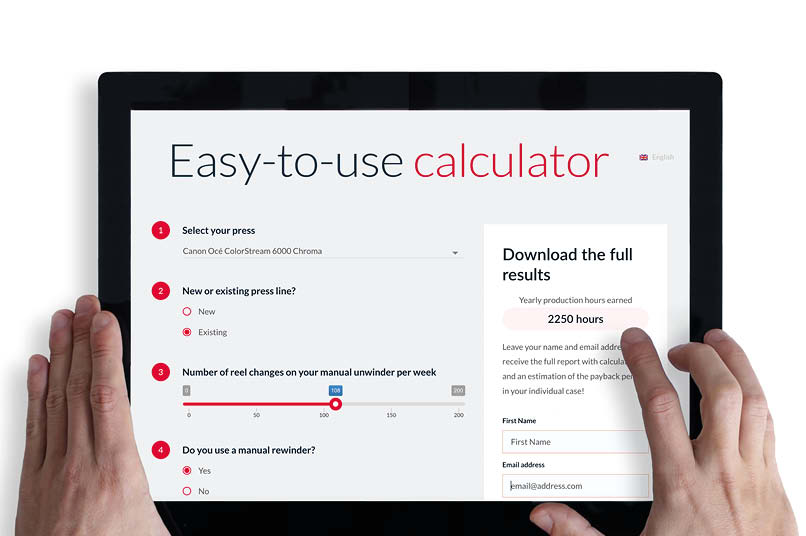
Frequently Asked Questions
Below you find the answers to some commonly asked questions about this equipment.
While increasing productivity is a primary reason for many printers to invest in non-stop auto splicing equipment, there are several additional benefits worth considering.
Firstly, incorporating auto splicing into press operations significantly reduces the manual effort involved. Press operators often express enthusiasm about auto splicing as it eliminates the need for laborious lifting and repetitive tasks. This, in turn, frees up time for operators to focus on other important responsibilities. The presence of non-stop auto splicing equipment can also make the job more appealing to potential new hires, contributing to the overall workforce attraction.
Furthermore, the CDN non-stop auto splicer delivers consistent and reliable joins between paper reels, minimizing the occurrence of failures and web breaks. This improvement in join consistency, compared to manual reel changes, leads to reduced waste in terms of slab and core material. By achieving more precise and dependable splices, the non-stop auto splicer helps optimize material usage and minimize waste generation.
Therefore, even if paper reel changes are infrequent, investing in non-stop auto splicing equipment can enhance operational efficiency, reduce manual labor, attract new talent, and improve overall waste management, ultimately contributing to a more productive and streamlined printing process.
The Contiweb CDN non-stop auto splicer has lift arms that can move up and down, allowing the reel to be loaded from the ground. This operation is ergonomic, and requires no lifting crane. Depending on the model, also no reel shafts are required.
The splice preparation for automatic splicing is a quick and straightforward task that only takes 2 minutes to complete. It can be easily performed, in a situation safe for the operator, while production is ongoing. The operator's involvement is minimal and involves applying a linear adhesive tape for the straight-tape splice on the paper. The time required for splice preparation is limited to the actual preparation process itself.
The Contiweb CDN non-stop auto splicer allows you to splice over to papers of different web widths, coatings and weights. This is very useful for short, fast-changing jobs. It is also easy to use rest reels.
The Contiweb CDN non-stop auto splicer is designed to create an overlap splice by default when joining two reels of paper. However, certain webfed inkjet printing presses may not accept the thickness of an overlap splice. In such cases, the CDN can be equipped with butt splice technology. This option allows for a thinner splice, addressing the compatibility requirements of these specific printing presses.
The illustration below shows two butt splices (left) and two overlap splices (right).
The Contiweb CDN non-stop auto splicer can handle paper reels with a diameter of up to 1,270 mm (50 inches) and a maximum weight of 1,600 kg. The minimum paper web width is 300mm. The maximum paper web width depends on the model.
Spare parts for Contiweb non-stop auto splicers are conveniently available in the Contiweb Parts Webshop. Sign up for an account and gain free access to Contiweb machine manuals and parts books, saving you valuable time by filtering your search for specific machine parts.
Plus, explore our Uptime Kits, specially curated with essential components to minimize downtime in the event of breakdowns, ensuring you have the necessary parts readily available in your own facility. Streamline your maintenance and keep your operations running smoothly with Contiweb.
Trusted by
Would you like to know more?
If you are interested in Contiweb's non-stop unwindings solutions and you would like to know more, then please don't hesitate to contact us!
Your contact
Rob Bosman
Sales Director
+31 6 51 20 27 55
sales@contiweb.com
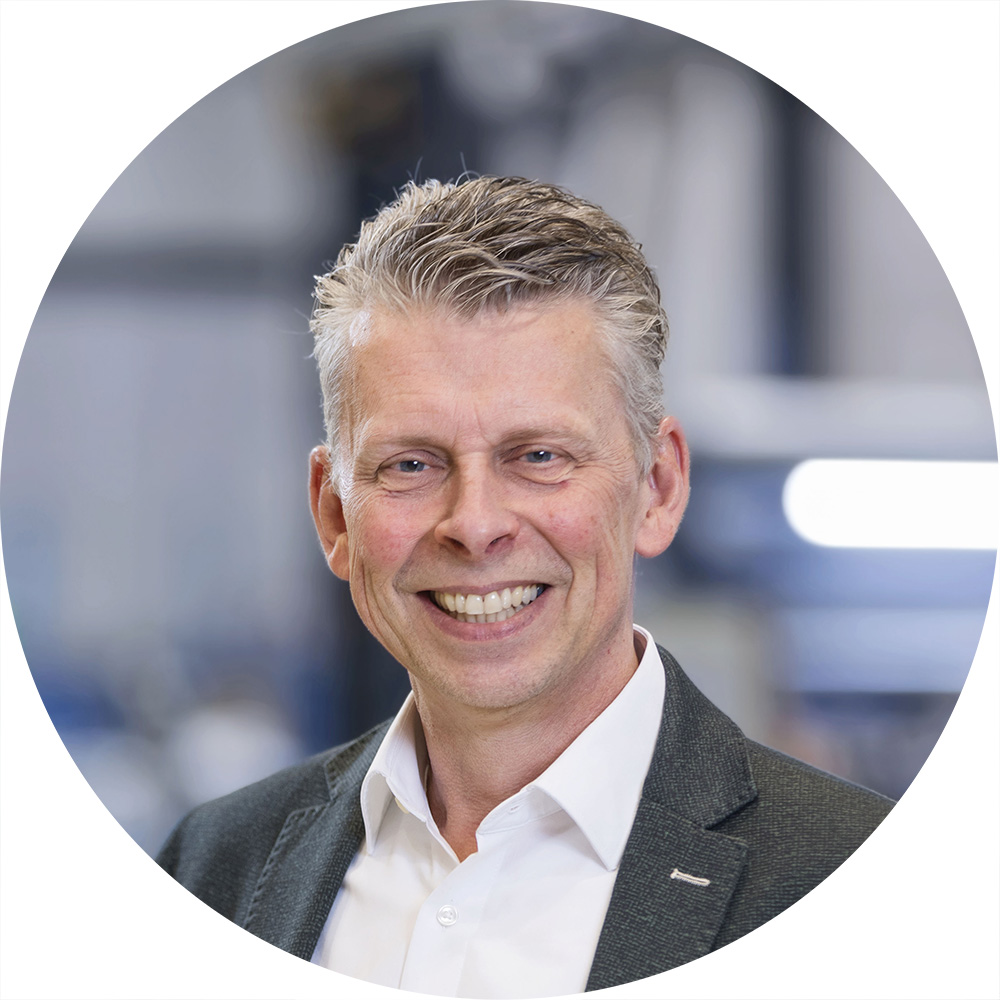