Burner Chamber Replacement
Replacement will pay for itself
Burner chambers are the heart of a Contiweb dryer, combusting the ink solvents at very high temperatures (800 C). This results in clean air emissions meeting the legal requirements to exhaust. By using efficient heat exchangers and low air flows, Contiweb manages to keep gas consumption low.
Burner chambers operate on high air speed and high temperatures. Heating and cooling lead to expansion of the steel of the burner chambers and give plastic deformation over the years. In average, the lifetime is between 12 and 15 years, which means the burner chambers should be regarded as wear parts that eventually will need to be replaced.
Towards the end of life the number of repairs increase and repair costs rise, CO in the exhaust can increase above legally permitted levels, or the required air flow can no longer be achieved. Most costly of all, unplanned burner downtimes need to be prevented from halting production. Periodical inspections and emission measurements indicate the condition of the burner chambers.
Energy efficient options
Over time Contiweb has improved the design of the burner chambers to be more robust. Contiweb will supply a fully functional replacement burner chamber that complies with the latest legislation. Dryers equipped with Contiweb’s Type C Chamber can be upgraded to Chamber C+ (1460 mm web width) or C++ (1680 mm or wider).
The C+ and C++ combustion chambers have a high-efficiency heat exchanger to save gas by recovering waste heat. In addition, the C++ chamber increases the machine lifetime. New burners and new hot air valves can be installed at the same time. So too can our Gas Reduction Enhancement (GRE) which further reduces gas consumption and reduces carbon footprint.
Savings depend on dimensions
Actual gas savings depend on the combustion chamber dimensions, your production run, and gas prices. Contiweb can calculate these beforehand.
The dryers have an upper and lower burner chamber, and both are preferably changed at the same time. The upper chamber can be changed on its own, but the lower chamber is also likely to be at end of life. And if the lower chamber is replaced, the upper chamber must anyway be removed.
Changing to a new burner chamber also involves installing new compensators, temperature sensors and critical ignition and flame monitoring parts. For C+ and C++ burner chambers, the bypass construction is renewed.
Installation time is between three and five days, needing four or five technicians depending on chamber size, selected upgrade and accessibility of the dryer workstation.
Benefits
- Comply to latest emission requirements
- Avoid unplanned downtime and production loss
- No more repair costs
- Gas savings
- Carbon footprint reduction
- Life time extension
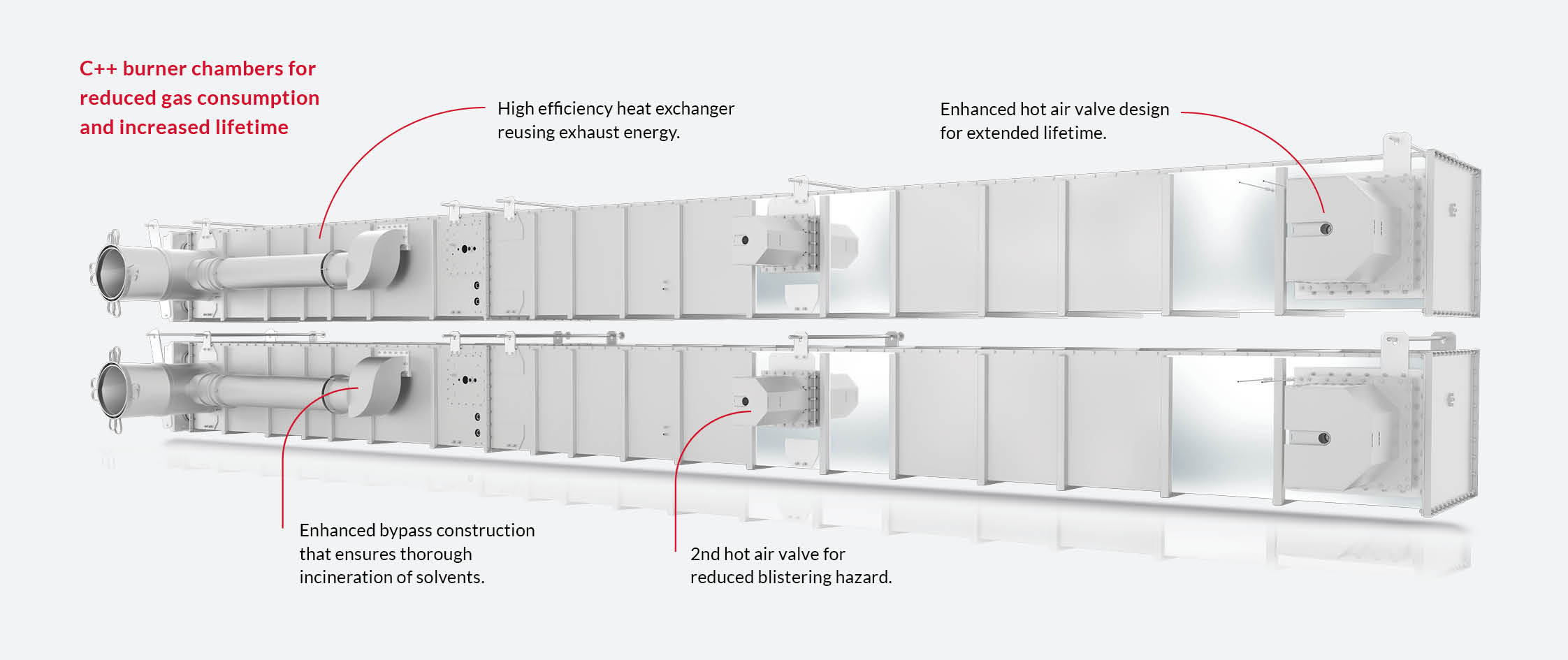
Would you like to know more?
If you would like to know more about this enhancement and you have additional questions, then please don't hesitate to contact us!
Sales contact
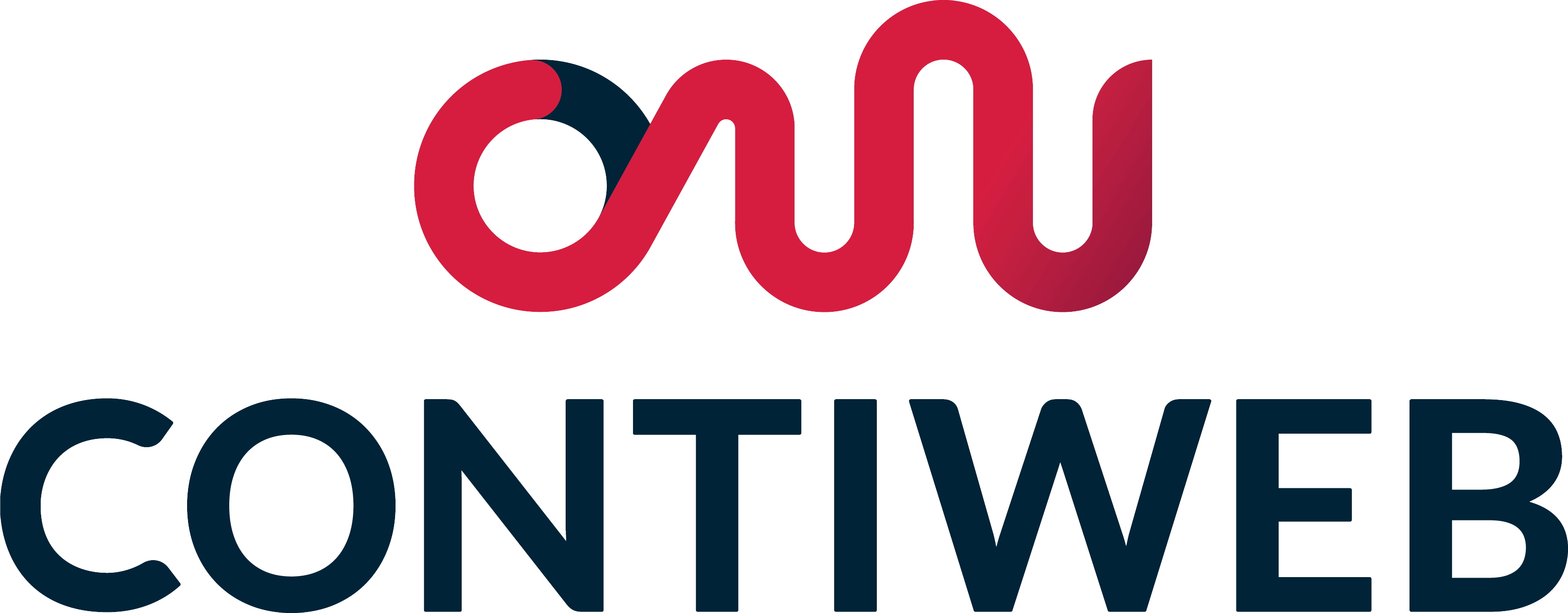
Download the product leaflet
The ongoing gas crisis means there is no more certainty of gas supply. Some of our customers fear losing access to gas completely, which could mean they cannot print anything with their current dryers. Our coldset enhancement option addresses this issue.
Fill out the form on the right to receive more information about this enhancement that lets you run coldset production on a heatset press without using natural gas.